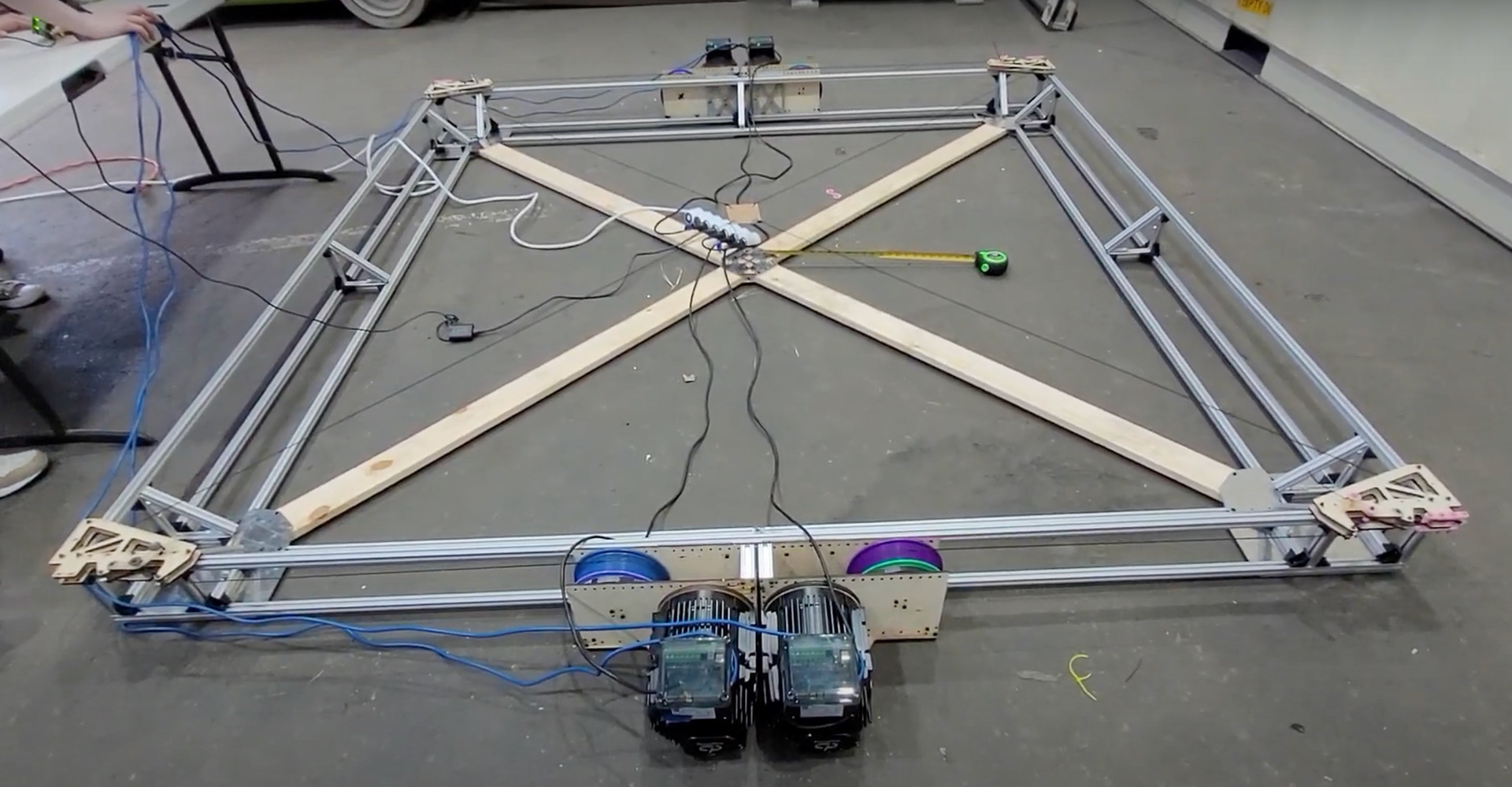
Introduction
Engineering Solution at Berkeley, in partnership with Sentien Robotics, developed a shipping container-sized 2D cable robot designed to accurately catch landing drones at high speeds. This project involved addressing both mechanical and software challenges, including designing, simulating, and manufacturing components for the winching mechanism and frame in CAD to handle high mechanical stresses at a large scale. On the software side, the focus was on implementing precise controls and using sensors with computer vision for 3D motion prediction. The purpose of this robot is to catch drones landing in their hive while the trailer is in motion.
Requirements
- 8 by 8 feet travel area
- Tension management system for accurate positioning
- Near instantaneous travel to accommodate moving trailer
- Low winch complexity for easy maintenance
- Budget of $3,000
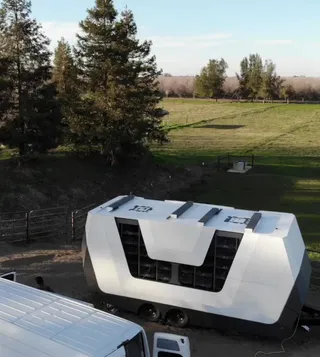
Features
The design features a robust 8 by 8 feet aluminum frame comprised of 2020 extrusions that was validated on FEA with a FoS of 2. To hold the extrusions together, 6061 aluminum brackets and HDPE plates were used. The robot also features an adjustable tensioning system to reduce error in payload location and greatly simply the code necessary. The bottom left illustrates the winch system which boasts of 4:1 HTD5 Belt Reduction and 9” Helical Winding Spool connected to the motor.
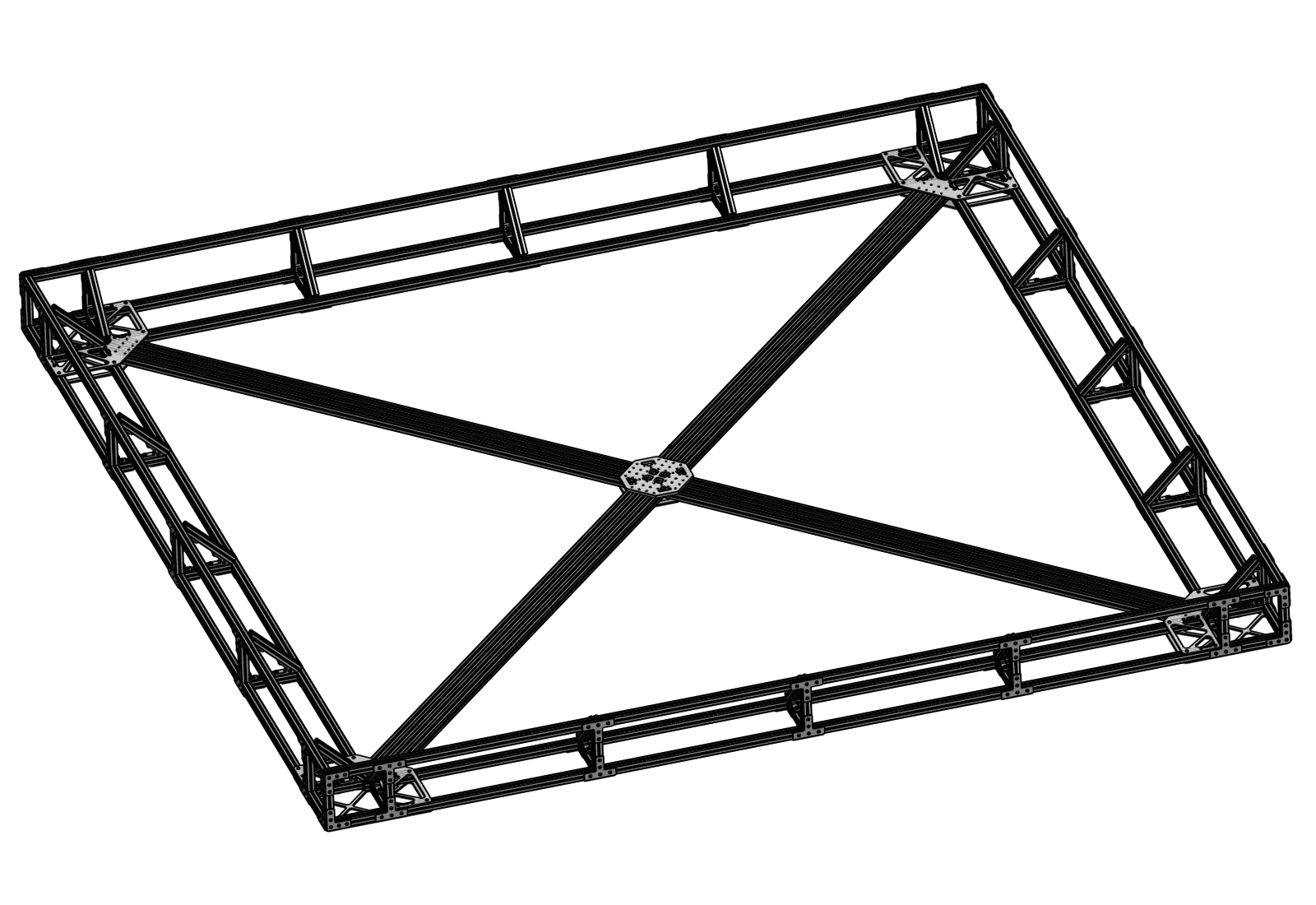
Aluminum frame with triangular braces
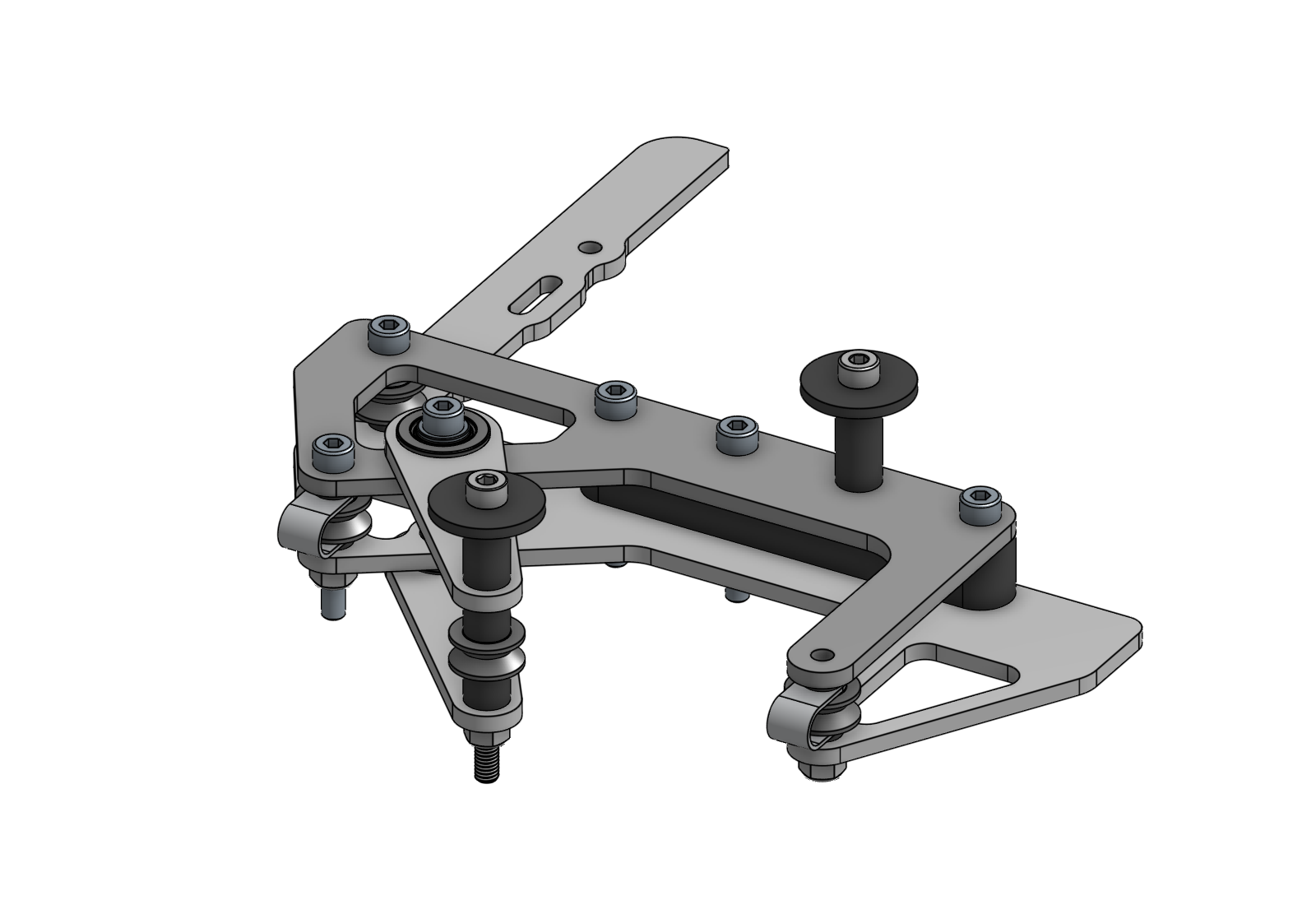
Tensioning system
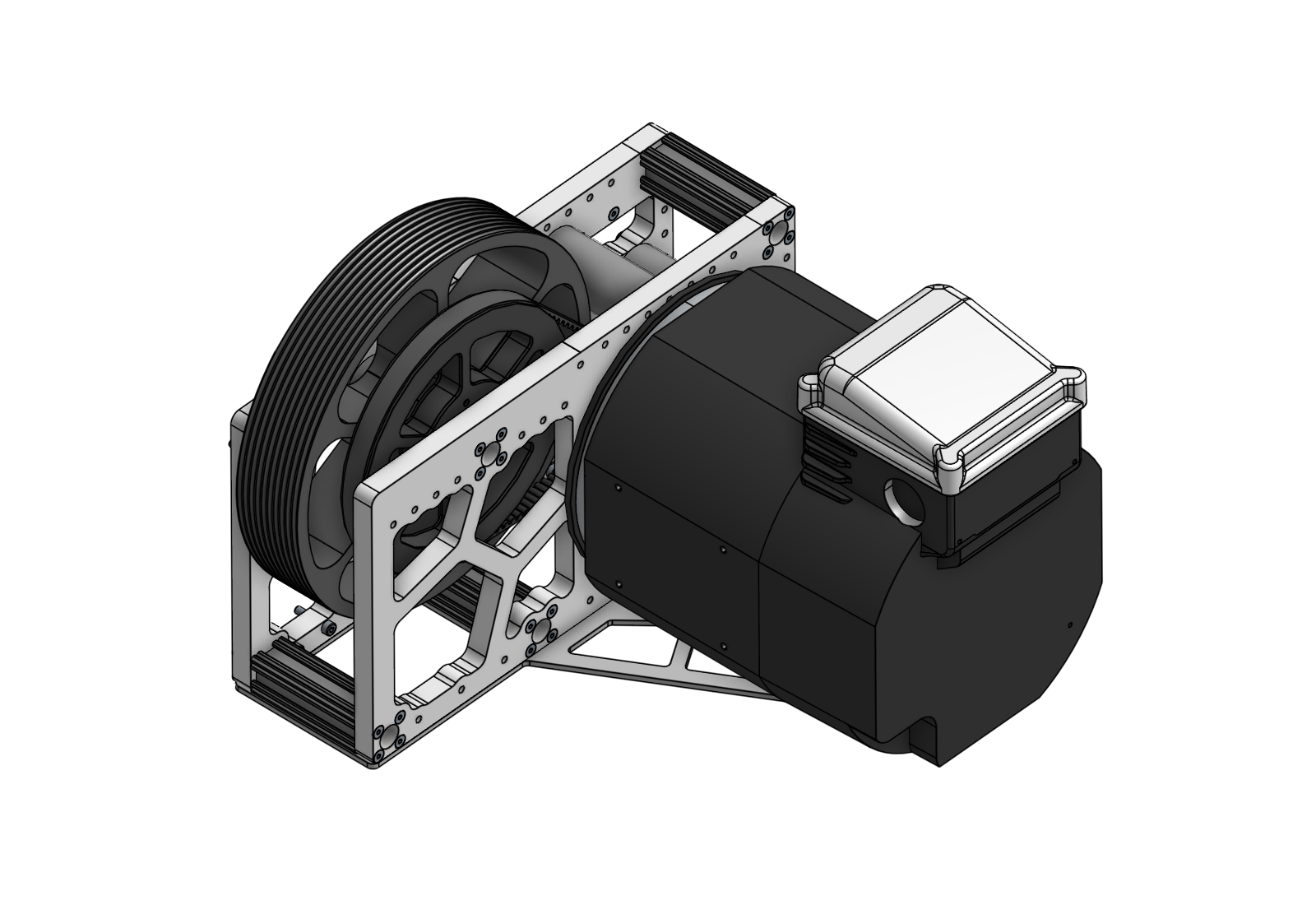
Winch system
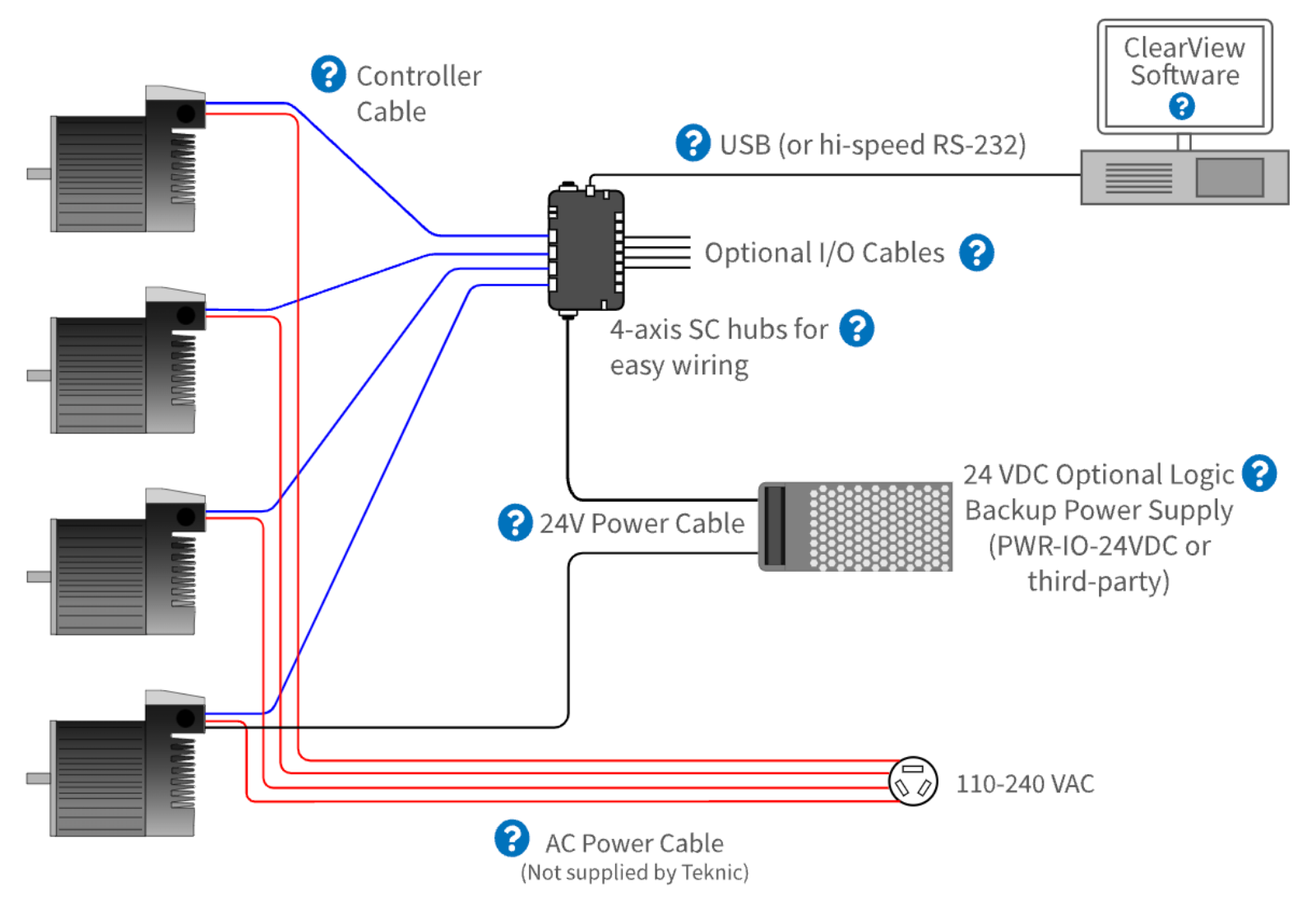
Software diagram
Conclusion
This project was super interesting and enabled me to combine mechanical design with electrical engineering. I particularly enjoyed solving the rope tensioning problem and building the actual frame. The large scale brought along some difficulties but seeing the cable robot all come together was extremely satisfying.
Skills learned: Working on the same part collaboratively, identifying bearings and designing around them, shortcuts in Onshape, code communicating with motors
Skills used: Onshape, Solidworks FEA, SC4 Hub, C++
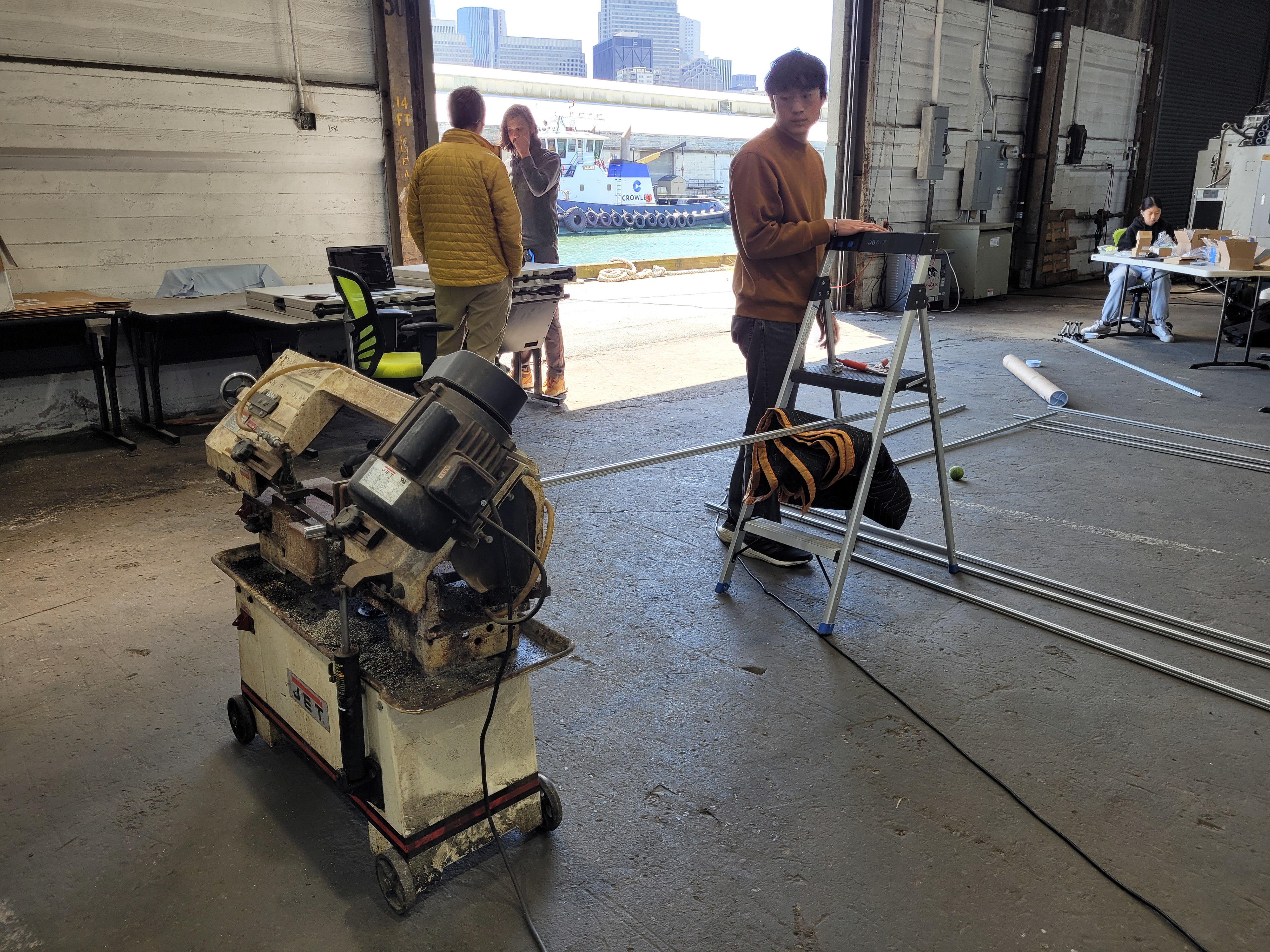